Are you a guitar enthusiast curious about the manufacturing process of Taylor guitars? Perhaps you’ve heard rumors that they are made in China and want to know the truth. As an avid musician and researcher, I have delved into the details surrounding Taylor’s production methods to give you all the information you need. In this article, we will explore where Taylor guitars are actually made, how their manufacturing processes differ from other brands, and what makes them stand out in the market. So if you’re ready to uncover the truth behind this beloved brand’s production, let’s get started!
So, Are Taylor guitars made in China?
Some Taylor guitars are made in China. However, the majority of their instruments are still made in the United States at their main factory in El Cajon, California. In recent years, Taylor has expanded its production to include a facility in Tecate, Mexico and a partnership with a factory in Indonesia.
Taylor Guitars prides itself on maintaining high quality standards for all of its instruments regardless of where they are manufactured. The company closely monitors and oversees the entire manufacturing process to ensure that each guitar meets their rigorous standards.
While some may view outsourcing as a negative aspect of a brand’s manufacturing process, it is important to note that this allows for more affordable options for customers without sacrificing quality. Additionally, by expanding production globally, Taylor is able to reach more markets and provide job opportunities for local communities.
In conclusion, while some Taylor guitars may be made in China or other countries outside of the US, the brand remains committed to producing high-quality instruments through careful oversight and attention to detail throughout every step of the manufacturing process.
Understanding Taylor Guitars: The Company History and Reputation
Taylor Guitars started out as a dream shared by two young men with a passion for music and craftsmanship. In 1974, Bob Taylor and Kurt Listug turned their aspirations into reality by establishing their own guitar company in El Cajon, California. With humble beginnings in a small workshop, they strived to create guitars that offered both exceptional sound quality and innovative design. Their philosophy was simple: blend modern technology with traditional techniques to craft instruments worthy of admiration.
Over the years, Taylor Guitars built its reputation on several key elements:
– Quality Craftsmanship: They use meticulous attention to detail to ensure every instrument is flawless.
– Innovation: From pioneering the bolt-on neck system to introducing environmentally sustainable practices.
– Customer Relationships: By fostering loyalty through excellent customer service and lifetime warranties.
Today, Taylor Guitars is celebrated globally for their finely tuned acoustics that resonate with musicians of all levels. Notably used by artists like Taylor Swift and Jason Mraz, these guitars have become synonymous with rich tones and unparalleled playability. Owning a Taylor means more than just possessing an instrument; it’s about being part of a legacy that values art, sound perfection, and environmental responsibility.
Bridging the gap between tradition and innovation has allowed them not only to stay relevant but also lead in an ever-evolving industry—a true testament to what dedication can achieve over decades.
The Manufacturing Process of Taylor Guitars: An Overview
Have you ever wondered how Taylor Guitars are made? It’s a fascinating process! Each guitar starts with selecting the finest woods. The company uses sustainable sources, like ebony and koa. They cut these woods into specific shapes for different parts of the guitar. This includes the body, neck, and fingerboard. All pieces must be perfect; any flaw could affect sound quality.
Next comes assembly, where skilled luthiers work their magic. Imagine craftsmen carefully gluing, sanding, and shaping each part by hand—it’s truly an art form! The guitars then go through rigorous inspections to ensure they meet high standards. After that, they’re polished until they gleam under light.
This is where technology meets craftsmanship. Advanced machines help in precision cutting while human hands oversee every detail.
– Cutting-edge techniques: Lasers and robots assist in intricate tasks
– Hand-finishing: Luthiers add personal touches
At last, the final steps include adding strings and tuning them to perfection before these beautiful instruments make their way from the workshop to musicians around the world.
The entire process reflects Taylor’s commitment to quality, blending modern tech with traditional methods—a harmony as sweet as their guitars’ tones themselves!
Read also: guitar method book 3
Distinguishing Features of Taylor Guitars: What Sets Them Apart?
Have you ever wondered what makes Taylor guitars stand out in the vast sea of musical instruments? One key aspect is their exceptional craftsmanship. Each guitar is built with meticulous attention to detail, ensuring a sound quality that both beginners and professionals can appreciate. The wood selection process at Taylor is rigorous. They use high-quality tonewoods such as mahogany, rosewood, and spruce which contribute immensely to the resonance and overall timbre of their guitars. This dedication to using premium materials guarantees that each guitar produces a rich, full-bodied sound.
Another defining characteristic of Taylor guitars lies in their innovative design features. Their unique neck profile ensures comfort during long playing sessions. Additionally, they ship many models with an advanced expression system for superior amplified sound quality—perfect for live performances or recording sessions.
Taylor’s commitment to environmental sustainability also sets them apart; they are pioneers in responsibly sourcing woods and reducing waste through efficient manufacturing processes.
Here’s why musicians love these specific features:
- Tone: Clear, balanced tones suitable for various genres.
- Playability: Comfortable necks designed for smooth action.
- Sustainability: Responsible wood sourcing methods.
So next time you hear someone strumming away on a Taylor guitar, remember it’s not just any instrument—it’s crafted excellence wrapped up in strings and wood!
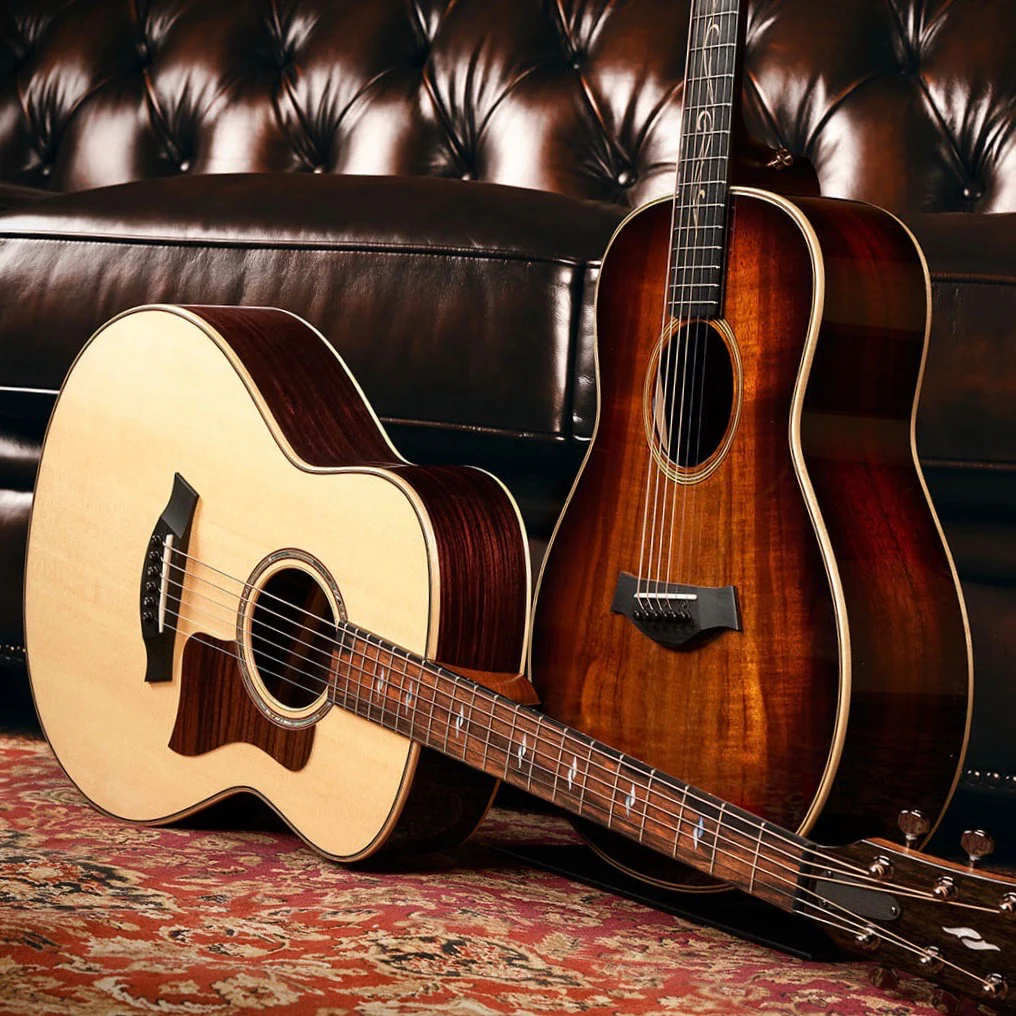
Where are Taylor guitars made? Addressing the China Question
Taylor guitars, renowned for their craftsmanship and quality, are primarily made in two locations: El Cajon, California and Tecate, Mexico. Their high-end models and custom shop creations are lovingly crafted in their state-of-the-art facility in El Cajon. This location boasts cutting-edge technology combined with traditional luthiery skills to produce some of the world’s finest acoustic guitars. The more affordable 100 and 200 series guitars come from the Tecate factory just across the border. Despite being made outside the U.S., these instruments still maintain Taylor’s attention to detail and commitment to excellence.
A common misconception is that Taylor manufactures its guitars in China, but this isn’t accurate. While many guitar companies outsource production to Asia, Taylor has chosen a different path ensuring control over every step of their process by keeping it closer to home. Moreover, both factories adhere strictly to ethical practices concerning labor conditions and environmental impact. Bob Taylor himself is a staunch advocate for sustainable forestry practices; as a result, they source wood responsibly while giving back through reforestation efforts around the globe.
– El Cajon: High-end models
– Tecate: Affordable series
With this approach, Taylor ensures each instrument not only sounds great but also carries a story of sustainability and craftsmanship behind it.
So next time you hold or play a Taylor guitar, remember, it’s not just an instrument—it’s art shaped with care right here on our continent.
You may also like: Is Simply piano 100% free
The Truth Behind the Production of Taylor Guitars.
Taylor Guitars, known for their impeccable sound and craftsmanship, have a fascinating production process that many people aren’t aware of. The journey begins with selecting the finest woods from around the globe. These woods are chosen not just for their beauty but for their tonal qualities. Each piece is carefully inspected to ensure it will produce the signature Taylor sound. The wood is then aged and dried to perfection, ensuring stability and resonance.
Once ready, these pieces go through a meticulous crafting process involving both advanced technology and skilled artisanship. Skilled luthiers hand-shape each part using traditional methods combined with precise machines that cut shapes based on computer models designed by Taylor engineers.
- The necks are made separately from the bodies.
- Bodies receive special bracing to enhance tone.
- Both parts undergo several refinements before being joined together.
The attention to detail doesn’t stop there; each guitar receives several coats of finish, which are sanded down between applications to achieve an ultra-smooth surface that’s as pleasing to touch as it is beautiful to look at. Finally, before leaving the factory floor, every guitar goes through rigorous testing where expert players verify its quality by playing various styles of music.
This ensures that each instrument leaving Taylor’s doors resonates with excellence.